
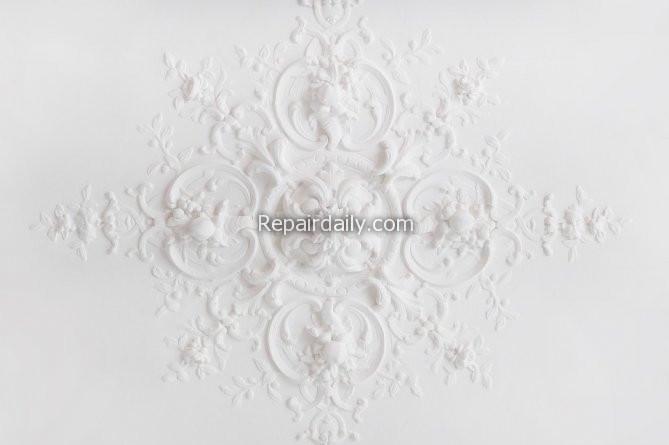
moulding
Over the last few years injection moulding has become a crucial manufacturing process for producing parts and products. Due to the very high adoption rate of this process by manufacturers, it provides customers with the many benefits of plastic injection moulding.
One of the main benefits is that it can produce a variety of parts quickly and in bulk. There are various types of injection moulding, with structural foam moulding and plastic injection moulding being the two best ones. We’ll look at the key benefits of choosing foam moulding over plastic injection moulding.
Why Structural Foam Moulding is Better?
Structural foam moulding is a low-pressure injection moulding process. It uses inert gas (such as a chemical blowing agent or nitrogen gas) to melted polymer before these two ingredients are injected into the mould.
What the gas does is it forces the polymer into the mould, it spreads out uniformly in the mould, therefore helping the polymer to take on the shape of the equipment.
Structural foam moulding is different from plastic injection moulding, because it can produce large structural parts and a higher quality of products. Structural foam moulding creates stronger products, excellent thermal properties and a high strength to weight ratio.
Low-pressure moulding helps to create parts that are structurally sound. This can lead to thicker wall sections with minimal warpage. And maybe the best bit of all, it can be created for less money than alternatives like expensive steel products.
The Benefits of Structural Foam Moulding
Some of these benefits include:
1. Improved Strength
A unique honeycomb structure is formed during structural foam moulding, creating renewed strength. That means that this process results in products and parts with a very high strength to weight ration, and this is higher when compared to conventional injection moulding.
2. Improved Aesthetics
Products and parts made with structural foam moulding has a more consistent and polished surface, and you can add the texture of your choice. It can help with the creation of intricate and thick parts and products that doesn’t have sink marks or depressions.
3. Variety of Mould Options
The low pressure of foam moulding allows for the use of economical moulding equipment tools, which leads to the mass production of multiple parts or very large parts.
It allows you the option of using aluminium moulds, which is not an option when it comes to conventional injection moulding.
4. Advantages
One production advantage is that it allows for different materials and colours to be moulded at the same time. A great design advantage is that you can use it to mould parts that weigh as much as several hundred pounds. And the main cost advantage is increased productivity and reduced cost.
5. Low Startup Costs
Foam moulding doesn’t need steel moulds, which leads to using less expensive and lighter materials. This means that your startup costs will be lower than if you were to choose conventional injection moulding.
I'm so excited to tackle all my home improvement projects! From plumbing to DIY and cleaning - I'm ready to get down to work! #homerepair #homecleaning #plumbing #diy #fixerupper #realestate #renovation #interiordesign #farmhouse #diy #homedecor #hgtv #home #farmhousedecor #modernfarmhouse #farmhousestyle #fixerupperstyle #fixandflip #homerenovation #realestateinvesting #beforeandafter #homesweethome #remodel #realestateinvestor #interior #realtor #joannagaines #flippinghouses #countryliving #design #homedesign #farmhouseinspired #investmentproperty #bhghome #renovationproject #farmhousekitchen #homeimprovement #farmhouseliving #cottagestyle #decor #realestateagent #magnoliahome #homeinspo #magnoliamarket #kitchendesign #dreamhome #shiplap #construction #houseflipping #investor #farmhousedesign #architecture #farmhousechic #homereno #rusticdecor #reno #kitchenremodel #webuyhouses #magnoliatable #rentalproperty #fixerupperinspired #newhome #interiors #homeremodel