
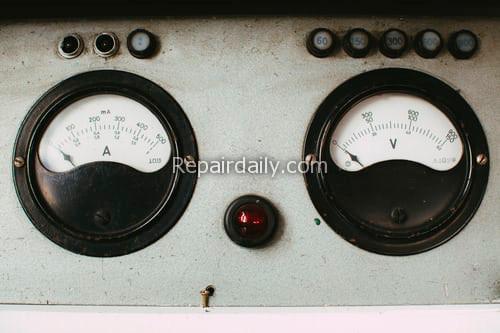
air compressor (1)
If compressed air is an integral part of your daily operations and downtime will cost you significant production losses. The question of whether to replace or repair a failed compressor is particularly important to you.
However, even though the choice in favor of repairing a compressor may seem to be a more economical option than buying a new compressor, it may not be the most advantageous choice in the long term.
Before we make a decision, let's consider a few factors. Cost is the main consideration, both directly and over time. Although a new compressor can be expensive, it is worth noting that when considering the cost of ownership over a ten year lifetime, the actual purchase price of a new compressor is only about 10% of the total cost. The actual cost of operating the compressor is your electricity bill! - is probably the main expense (about 75%).
Other factors that will affect your decision to repair or replace your compressor include the age of the compressor, its energy efficiency compared to newer models, its previous repair history, and overall reliability.
Repair Versus Replacement
Before choosing a new compressor over your existing one, it is wise to check the system thoroughly first, just in case the failure is due to something that can be easily corrected.
Your compressor may have broken down for many reasons, and not all of them indicate irreparable damage or repair problems! Your local service technician can help.
Some factors that are important for compressor repair include:
- It's relatively new and hasn't worked many hours yet.
- It has not yet been primarily replaced by new technology.
- It's a model for which spare parts are easily available.
- It is usually reliable, and repairs are not indicative of major problems that may arise in the future.
On the other hand, replacing a compressor may be the most viable solution in such circumstances:
- If it broke once, it's likely to happen again.
- Compressors are becoming more energy-efficient all the time, so the cost of a new one may soon pay off by saving energy.
- If your compressor is an old model, finding spare parts for it can be more complicated, expensive, and time-consuming
- Your older compressor may be too small for your company's current needs. Therefore, replacing it with a larger unit may be an ideal opportunity for your future business.
Are New Compressors Expensive?
Yeah, new air compressors can seem very expensive at first. However, when factoring energy savings, possible energy credits from your power supplier increased reliability, and reduced maintenance costs, the payback period is often shorter than you think.
The initial cost also does not take into account the potentially devastating downtime costs associated with compressor outages
Calculating the life cycle cost of an air compressor before buying new equipment is a smart way to analyze the total investment. Life-cycle costing can also be used as a comparison tool when checking other products and systems.
Therefore, help identify other important installation requirements and assess potential environmental, energy-saving, and increased product quality requirements; and identify areas where energy efficiency can be improved.
DIY Air Compressor Repair
There are three major fixes that you can make yourself. Most faults fall into one of these three categories.
Remember that high-pressure air compressors can burst if the tank is damaged. Leave this complicated repair to professionals. However, to save money, find a new one to replace your air compressor tank.
Step 1. Safety First!
Before starting the overhaul of the air compressor, it is necessary to disconnect the power supply and clean the tank from the remaining air. It is easy to remove the power supply, just unplug it from the socket.
Cleaning the tank may not be so obvious. To clean the tank, put a ring on the safety valve. If the tank is half full, the noise of the rushing air can be loud as it is washed out of the openings of the safety valve, so be careful!
Step 2. Set Up A Work Area
When working with an air compressor, set the appropriate working area. You can use a couple of folding tables that you have around for parties.
Assemble all the necessary tools as well as plastic containers to store discrete parts. Also, spray the WD40 grease, paper towels, and maybe spray a bottle of water to check for leaks.
Step 3. Remove Compressor Shroud
The motor and compressor unit is enclosed in a two-component plastic casing. The smaller front casing is mounted to the compressor with two Torx screws. The rear case is mounted to the motor with one Torx screw. The front and rear cases are connected to the integrated clips.
The case serves several purposes. It prevents the air compressor head from being touched, which can become hot during use. It protects you from cuts in the blades of the built-in cooling fan and also isolates you from contact with electrical parts such as the motor and starter condensers.
Step 4. Remove The Compressor Head
Remove the compressor head. It is held in place by four bolts. The black plastic part on the right is called a silencer. It is the place where the air enters the compressor. I think it "silences" the sound of air rushing into the air intake.
Step 5. Valve Plate Assembly Removal
When the compressor head is removed, the valve plate block opens. It allows air to enter the compressor but prevents air from escaping through the suction silencer.
Step 6. Valve Plate Assembly Inspection
Disassemble the valve plate assembly. The metal reed is held in place by small bolts. Check reeds for deformation or cracks. They should provide a good seal on the valve plate so that the air compressor reaches maximum pressure.
Step 7. Fan Removal
The fan is connected to the end of the motor shaft and held in place by one bolt. The fan must be removed to loosen the bolt holding the connecting rod to the shaft.
Step 8. Connecting Rod And Cylinder Sleeve Removal
After removing the fan, the connecting rod should be removed from the bearing with one bolt at the base. The cylinder sleeve is kept in place by the valve guide and head.
Since the valve head and guide are removed, the cylinder bushing can be easily removed by pulling it straight up and out. Once the cylinder bushing has been removed, the connecting rod can be removed.
There's a counterweight under the connecting rod. It is essential to maintain the orientation of the compensation concerning the connecting rod, which will cause excessive vibration.
On some compressors, the counterweight is indicated with the connecting rod at the bottom of the stroke.
Step 9. Cylinder Sleeve Inspection
Check the cylinder bushing for damage. It is clear that there are scratches and scrapes on the walls of this cylinder bushing, and it must be replaced.
Disassembly and control of the pressure switch, before starting work, to make sure that the air compressor is de-energized!
The pressure switch is a black box located to the left of the pressure gauges. It switches the compressor motor on and off to maintain tank pressure.
Step 10. Removal Of The Check Valve
The non-return valve is located on top of the tank at the end of the motor. Two aluminum lines are connected to it. These lines must be removed, and the non-return valve can then be unscrewed from the tank using a large crescent spanner.
Step 11. Check Valve Inspection
When the compressor is switched off, the non-return valve stops the air coming out of the tank and discharges the pressure in the discharge line through a small pipe. This pipe connects to the pressure switch and releases air there.
If the check valve is jammed, air can flow through this pipe, which causes the compressor to disconnect from the electrical switch during replenishment or re-processing.
The non-return valve simply moves in and out, but most importantly, it should be sealed when closed. If the motor is running normally and it takes a long time to build up the pressure, and the cylinder bushing looks good, then this is likely a problem with the check valve.
Naturally, you can clean the check valve by taking it out of the tank and flushing the WD40 several times. If the WD40 does not seem to be working and you still have a problem with the pressure build-up in the tank, then this part should be replaced.
Step 12. Replacing The Connecting Rod And Cylinder Sleeve
Most sets of connecting rods and cylinder bushings come with replaceable gaskets used between the head and cylinder. Besides, detailed instructions, including bolt torque specifications, are provided.
Step 13. Reassembly
Mounting the air compressor is quite simple. If you follow the above steps in reverse order, your air compressor should function like it did the day you bought it. Note that it is crucial to replace the cylinder and head gaskets during assembly.
Step 14. Testing
It is crucial to test the reconstituted air compressor after assembly. Connect it, switch it on, and allow it to rise to peak tank pressure. Once the tank pressure has peaked, switch off the pressure switch, and unplug it from the outlet.
Listen to the hissing sound of the air coming out of the joints. Spray some water around joints to detect small leaks. Thoroughly dry out the air compressor before turning it back on. If leaks are detected, try to repair them by tightening the connection.
If this does not help, it may be necessary to clean the tank, remove the leaking part, and apply some car sealant to the threads to form a tight seal.
Return to the leak test after the part has been screwed back onto the air compressor and tightened properly.
To Sum Up - Is It Worth Repairing Your Air Compressor Yourself?
You can also troubleshoot and repair the air compressor. Why not, parts are often available, and air compressors are relatively simple appliances to repair.
Repairing an air compressor can potentially save you hundreds of dollars, compared to the cost of a new one.
If you follow the repair steps that have been suggested in this article your compressor could be as good as new!
I'm so excited to tackle all my home improvement projects! From plumbing to DIY and cleaning - I'm ready to get down to work! #homerepair #homecleaning #plumbing #diy #fixerupper #realestate #renovation #interiordesign #farmhouse #diy #homedecor #hgtv #home #farmhousedecor #modernfarmhouse #farmhousestyle #fixerupperstyle #fixandflip #homerenovation #realestateinvesting #beforeandafter #homesweethome #remodel #realestateinvestor #interior #realtor #joannagaines #flippinghouses #countryliving #design #homedesign #farmhouseinspired #investmentproperty #bhghome #renovationproject #farmhousekitchen #homeimprovement #farmhouseliving #cottagestyle #decor #realestateagent #magnoliahome #homeinspo #magnoliamarket #kitchendesign #dreamhome #shiplap #construction #houseflipping #investor #farmhousedesign #architecture #farmhousechic #homereno #rusticdecor #reno #kitchenremodel #webuyhouses #magnoliatable #rentalproperty #fixerupperinspired #newhome #interiors #homeremodel