
Garnet Abrasives and Garnet Recycling Systems: Correct Method of Selecting Good Quality Garnet and the Correct Recycling Procedures
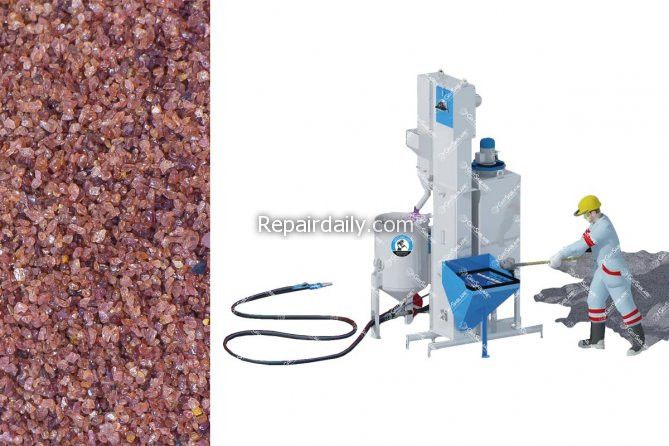
Garnet Abrasives
The purpose of the below technical overview is to identify the major components of effective equipment for recycling garnet abrasives. Also covered are several rules of recycling that are critical to understand when recycling garnet (or any non-ferrous abrasive). Lastly, how to monitor the effectiveness of a recycling operation is explained. Following these guidelines can help ensure that each blast with garnet abrasives from GritSablare Abrasives is as productive as the first.
1. Key components of effective Garnet recycling equipment
The most important component of any recycling system is the method used to separate and classify the used abrasive. Experience has shown that systems which utilize a gravity fed air-wash such as the ProFlo or UltraFlo by GritSablare Abrasive recycling systems are very effective for recycling garnet. A coarse particle screen below the air-wash has proven itself useful for removing additional contaminants and improving the level of cleanliness of the recycled garnet. Other major components of a typical recycling system include a loading hopper, bucket elevator, integrated storage hopper (to store recycled abrasive) and a reverse pulse cartridge dust collector. Depending on the application, a level of cleanliness of 90-95% should be possible.
2. Overview – Recycling GritSablare Abrasives Garnet Efficiently
The goal of recycling is to clean the blasted abrasive so it can be used again productively. Ensuring that the recycled abrasive (known as the “correct abrasive mix”) is clean and contains abrasive particles with the appropriate size range involves two basic operations: the removal of oversized and undersized contaminants and the addition of topping up with new abrasive. In order to accomplish this efficiently, both the blasted and new abrasives makeup garnet must be kept dry.
Correct recycling of the blasted (used garnet) abrasive is accomplished by air-wash separation. A loading hopper screen removes the large contaminants such as large paint chips, rust, welding rods and work site debris. An air-wash separator unit, working in conjunction with a dust collector, removes unwanted fine garnet abrasive particles.
The most critical element of the recycling process is the creation of an effective “abrasive mix” which is comprised of a range of small, medium and large garnet particles. Given that a portion of the garnet breaks down each time it is abrasive blasted after striking the surface to be blasted, a productive working mix should be created by adding a percentage of new abrasive to the cleaned abrasive at a rate equal to the rate of garnet particle breakdown. These additions should be made at regular intervals and be based on the amount of fines extracted by the separation unit, daily visual inspections of the recycled garnet abrasive.
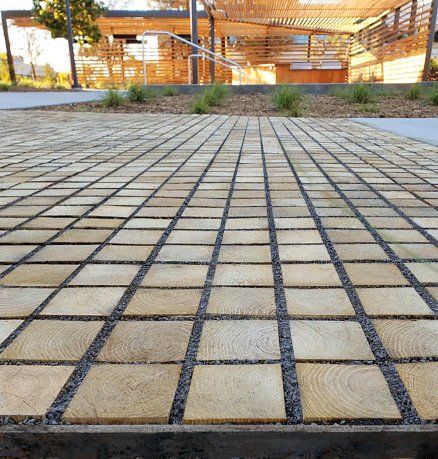
GritSablare
3. Adjustment of the GritSablare recycling equipment
Both the ProFlo and UltraFlo abrasive recycling systems utilize a correctly size air-wash separator because they can be precisely adjusted to extract fines from the dirty garnet abrasive. It is important to use a system with a properly designed air-wash. A well-designed air-wash separator works much like a vacuum cleaner. A thin curtain of dirty garnet abrasive slips under a swinging baffle and then passes through the air-wash. The air flow (or suction) created by the dust collector pulls fines and airborne dust into the dust collector. Heavier fines are also then removed away by a lower separator lip.
It is critical to remove as many fines as possible during each recycling operation. Excess fines can reduce productivity, create unwanted dust during the abrasive blasting application, reduce the blasting operators visibility and critically reduce the blasted surface profile.
4. The “Correct GritSablare Abrasives Garnet Mix”
A properly balanced particle size distribution in the garnet abrasive working mix is the key to effective and efficient abrasive blast cleaning. A good working mix contains a well-balanced distribution of large, medium and small abrasive particles. Large particles perform the major task of loosening the thick, heavy contaminants (mil-scale or heavy high-build coatings). Small particles provide the coverage (speed of blasting) necessary for the efficient removal of lighter coatings, mill scale and rust. Smaller particles also perform the important task of thoroughly cleaning and cleaning of any valleys on previous blasted surfaces and to ensure any slight surface deviations or pits are cleaned to meet the surface standards of SA 2.5 or SA3 as required for the project.
Establishing a suitable range of particles in the working mix is dependent of the individual project requirements and is based primarily on the surface profile requirement and the coating or contaminants to be removed. Typically, red garnet particles smaller than 80-90 mesh should be extracted from the working mix by the abrasive recycling system when removing high-build coatings (such as glass flake) or medium rust. For blast applications removing light rust, mill scale, primers and thinner coatings, the working mix can be broadened to include 100 or even 120 mesh garnet particles.
Each abrasive type, size and shape has its own impact life cycle (particle breakdown rate). Each time an abrasive is blasted a portion of the particles break down. The amount of air pressure used to blast also naturally effects the breakdown rate. Generally, it is expected a 20 – 25% breakdown rate at 90-110 PSI at the nozzle with GritSablare Abrasives grade 30/60 Mesh. As a general rule, it is recommended to add back 25% of new garnet abrasive with each recycle unless a shallow surface profile is required for the project.
New garnet abrasive should be added into the working mix at approximately the same quantity as what is discharged out by the recycling system. Example, for every 20 tons of garnet abrasive blasted and collected, approximately three to four tons will break down to either dust or non-usable fine particles.
New Garnet abrasive can be added via the abrasive loading hopper at the bottom of the bucket elevator on either the ProFlo or UltraFlo Abrasive Recycling Systems to ensure correct mixing of the previously blasted and new abrasive mix. Not adding new abrasive decreases the percentage of coarser size particles in the operating mix and leads to slower cutting, increased dust and reduced blasted surface profile.
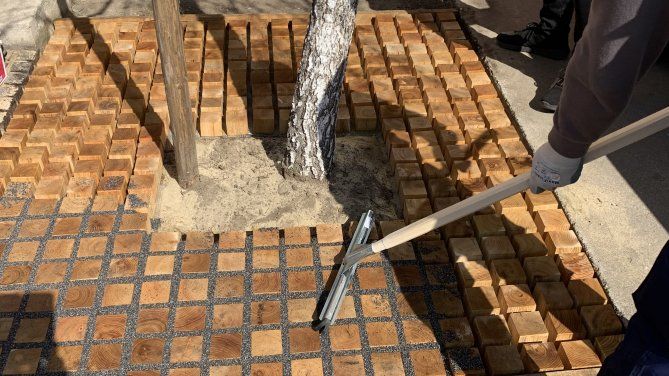
GritSablare
5. Monitoring efficiency of GritSablare Abrasives Garnet
The recycled abrasive should be checked to ensure that the Recycling System is removing both oversized coarse contaminants – if using GritSablare Abrasives 30/60 mesh (typically 20 mesh or larger) and the fines (typically 80-90 mesh or smaller). The abrasive discharged from the air-wash separator (into the dust bin) should be checked to determine if usable abrasive are being improperly withdrawn from the garnet working mix. Abrasive samples should be taken directly from the air-wash as the abrasive falls past the internal baffle and from the air-wash discharge tube.
A “rule of thumb” method that we do offer our large end-user customers is to select the “critical” screen for the blasting application where recycled garnet is being used. Example, to check for excessive fines in the working mix, use a single #80 or #100 mesh screen. To check for too much useable garnet being extracted by the air-wash separator, use a single #60 mesh screen. This will give a relative indication of how well the recycling process is being managed and point out any potential problems.
Routine visual checks should also be made by qualified blasting and site personnel at the discharge tubes leading from the air-wash, which we recommend to be conducted approx. 2-3 times per shift. GritSablare provides to its customers complete recycling and cleaning systems for blasting waste, and also, an exhaustive offer of blasting materials, which include: garnet, copper slag, steel grit, stainless steel grit, electrocorundum, glass beads.
I'm so excited to tackle all my home improvement projects! From plumbing to DIY and cleaning - I'm ready to get down to work! #homerepair #homecleaning #plumbing #diy #fixerupper #realestate #renovation #interiordesign #farmhouse #diy #homedecor #hgtv #home #farmhousedecor #modernfarmhouse #farmhousestyle #fixerupperstyle #fixandflip #homerenovation #realestateinvesting #beforeandafter #homesweethome #remodel #realestateinvestor #interior #realtor #joannagaines #flippinghouses #countryliving #design #homedesign #farmhouseinspired #investmentproperty #bhghome #renovationproject #farmhousekitchen #homeimprovement #farmhouseliving #cottagestyle #decor #realestateagent #magnoliahome #homeinspo #magnoliamarket #kitchendesign #dreamhome #shiplap #construction #houseflipping #investor #farmhousedesign #architecture #farmhousechic #homereno #rusticdecor #reno #kitchenremodel #webuyhouses #magnoliatable #rentalproperty #fixerupperinspired #newhome #interiors #homeremodel